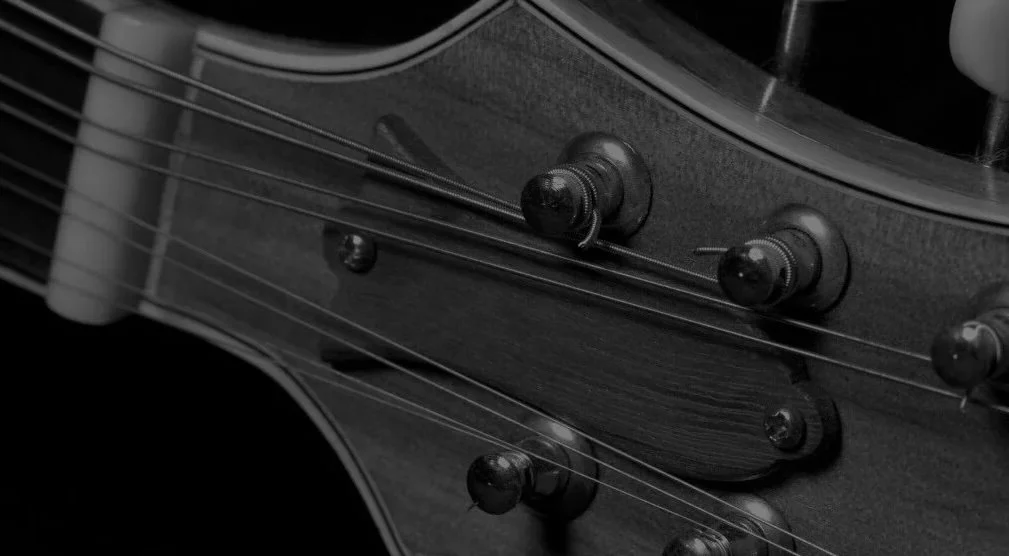
BLOG
TIME FOR A CHANGE
Most guitar players are traditionalists. They like familiar shapes and colors. Take for instance the 1950’s Fender Stratocaster and Telecaster, their most popular 6-string models. Fender is in competition with itself to keep producing these same models no matter how hard they try to improve it. Over the years as trends change, Fender has tried to keep up with that change by adding things like a humbucker pickup, locking tuners, a Floyd Rose bridge, and so forth. But in the end the 1950’s Stratocaster and Telecaster shape is their winner. I myself jumped on the band wagon and made Stratocaster style and Telecaster style guitars using highly figured 1/4” drop tops, semi-hollow bodies, Paul Reed Smith type natural bindings, triple P-90 pickups and fancy stains and tints. Something that Fender did not provide. The closest offering they had was the Fender Foto Flame which used a thin sheet of photographic film glued to a wood body and most people thought it was a solid wood top. It looked cool because we like the beauty of highly figured wood on our guitars.
The latest guitar trend these days is a super light body (around 6 pounds) with a few pointy ends and 7 or more strings. Don’t forget the stainless steel fan frets, kill switches, thick colorful polyurethane finishes and super overwound pickups. Keeping up with trends is hard and I myself have chosen to no longer ride on that bandwagon. As fun as it was, I also felt uncomfortable building copies of Fender guitars rather than my own shapes and designs. It wasn’t original. It was a copy. Therefore I have recently made the decision to stop building the usual S-Style and T-Style electric guitars and focus more on the craftsmanship and tone shaping of acoustic guitars and mandolins.
There are going to be a few changes in the shop. I’ll still continue doing repair work, but I’ll be building more acoustic guitars and mandolins using traditional hand tools and methods that I truly enjoy. There will be more options for tone woods and design choices for the different styles of playing such as finger style, bluegrass or Celtic.
Another change I would like to make is teaching and sharing knowledge. I am hoping to find someone I can teach how to do repair work and instrument building. There is knowledge that needs to be passed along to the next generation. The ideal exchange would be a person that has the skill set and in-depth experience with video creation and photography to help train me on navigating social media and promoting my business. If you know of anyone, please send them my way.
Thanks for taking the time to follow along.
How to Setup your Guitar
I believe that every musician should be able to do a full “setup” on their own instrument. However, if you’re not comfortable or don’t have the proper tools, I can help.
What’s involved? Will it really make your guitar play better? And is it possible to do it yourself, or should you leave it to a pro?
A setup is actually a series of procedures, many of which fall under the categories of “basic maintenance” and “fine adjustment.” Much like a car’s seasonal tune-up, a setup should be performed to address the changes a guitar undergoes over time, with adjustments made to the instrument in order to match your preference of strings, pickups and playing habits. A setup can also reveal potential problems before they become major headaches.
These are the steps that I will perform doing a complete setup once the guitar is brought up to pitch.
1. Adjust the Truss Rod for Proper Neck Relief
Virtually every acoustic and electric steel-string guitar built after the mid-Seventies has an adjustable truss rod, which runs the length of the neck and counteracts the tension of the strings to help keep the neck straight. Loosen it, and the strings pull the neck into a concave bow, resulting in more relief—i.e., the distance between the strings and the fretboard. Tighten it, and the neck bends backward—this is called back-bow—against the natural curve the string tension imparts, moving the strings closer to the fretboard. Neck relief varies depending on the style of playing and the type of playing. I usually adjust to around .006” at the 6th fret on acoustic guitars, .008” at the 8th fret on electric guitars and .014” at the 8th fret for bass guitars.
2. Adjust the Bridge Height
A guitar’s action should be adjusted at the bridge, not the truss rod. On an electric guitar, this is a matter of twisting the appropriate screws; on an acoustic guitar, you may have to shim or sand the bridge saddle.
Depending on the playing style of the player, the type of instrument and the fretboard radius, these are the measurements I’m aiming for. On an acoustic steel string guitar the high E - 5/64”, low E - 6/64”. On an electric guitar high E - 2/32” and low E 3/32”. However, every player style is different and requires their own unique setup.
The key is to not have any fret buzz up and down the neck as the guitar is played.
3. Check the Nut Height
With the truss rod and bridge fine-tuned, we enter the final phase of action altering. Although these days, the vast majority of nuts are well made, even some expensive production guitars can slip through the cracks with nut slots cut a bit too high or too low.
If any open string buzzes, its string slot is low and the nut must be shimmed up or replaced. Of course, this means the other slots must be deepened to compensate for the higher nut.
All nut slots get lubricated with graphite powder to help prevent string binding.
4. Check the Electronics
Do your switches snap, crackle or pop? Does it sound like someone’s frying bacon every time you do a volume swell? A good setup includes checking a guitar’s electronics. For amplified acoustics as well as electrics with active pickups, this means a battery check (and, if necessary, replacement). Also, all the nuts and screws that anchor the guitar’s electronics should be tightened. I use De-Oxit Cleaner to clean and lubricate all pots and switches. If the cleaner doesn’t eliminate the excess noise, then it’s time to replace that component. Finally, I tighten and clean the output jack.
5. Change the Strings
All of the adjustments discussed so far are done prior to changing strings. The only time you would adjust the truss rod, bridge height and nut slots with new strings on your guitar would be when changing to a different gauge. Once the strings are changed, I stretch each one to tighten the post wraps. This will help the strings stay in tune longer. A new set of strings will also make your guitar sound better as well.
6. Check the Tuning Machine Hardware
All tuners are checked, screws tightened, tension adjusted and gears lubricated. I typically do 2 1/2 string wraps on the tuner post.
7. Clean and Check Frets
All frets are checked for level and cleaned. Any high spots or divots are leveled and crowned. Sharp edges are filed away. All setups include up to 20 minutes of fret work. However, for the lowest action possible, your guitar may require a complete fret level and crown. That is above and beyond a routine setup and requires a different procedure.
8. Clean and Oil the Fretboard
Just like polishing the frets, the fretboard is also cleaned with Naphtha followed by a small application of Lemon Oil to moisturize the wood. Lemon Oil is also applied to an unfinished acoustic guitar bridge.
9. Inspect for Structural Problems
Just as string tension can hide loose tuning gears, it can hide loose joints and cracks. Bolt-neck electrics occasionally suffer from lose neck-joint screws, and braces within an acoustic guitar sometimes break or come unglued. All guitars are inspected for potential structural problems.
10. Adjust the Pickup Height
Pickup height is adjusted for balanced output.
11. Set the Intonation
Intonation is adjusted for proper pitch up and down the fretboard.
12. Tremelo Adjustment
All tremolos, Fender Strat style, Floyd Rose, etc are adjusted for proper tension and all metal contact points are lubricated.
13. Clean and Polish
The finishing touch! A cleaned and polish guitar just begs to be picked up and played, and that’s what it’s all about.
14. Warranty
All setups performed by Keeley Guitars comes with a 90-day warranty. If a buzz develops or the truss rod needs a fine adjustment, I’ll do that for free. Each setup comes with a warranty card.
If you’re comfortable doing a setup yourself, then GREAT! If you need help and would like to have me do a setup, then please give me a call to schedule an appointment (509) 738-6491.
Thanks!
Photo: 1959 Gibson LG-1 and a 1925 Martin 0-18.
An Article by Gabriel Cruden, Publisher for the North Columbia Monthly
I have a 12-string guitar that belonged to a musician friend. It was given to me by his widow after he passed away at a young age from cancer in the late 1980s. The guitar had been his constant companion during his travels, from his home country of France, to Hawaii, and beyond. During his illness, the guitar was left out one evening in its case, but the case was not buckled shut, and when picked up, the guitar fell out and snapped at the top of the neck. In gifting it to me, it was hoped I might someday repair and make music with it, carrying on his memory.
A couple of decades later I did an apprenticeship with Dave Keeley, a master luthier in Kettle Falls, so that I could learn how to repair the guitar, and learn something of the craft. Dave’s shop was small and stacked to the low ceiling with raw wood, shelves full of tools, and instruments in various stages of construction and repair. Tucked in here and there were old-fashioned radios and electronic testing gear. And a workbench. It smelled of wood and pipe tobacco and varnish. It was amazing how much fit in that tiny space, yet it was meticulously organized and felt enfolding rather than cramped, like a cocoon where instruments were transformed from the wood.
Building a musical instrument takes time – a lot of time. And I remember one evening, while waiting for a piece to dry, we were talking about how we spend our time. Dave took out his tape measure and, using inches, approximated the average male life-span and then, sliding the tape measure in, deducted his age, average time sleeping, average time at work, and so on, and all the while the extended tape measure got shorter and shorter. This made an impression.
I thought too about the Frenchman whose guitar we worked on, how the measure of his life was cut so short. I thought about how precious and fleeting life can be. And I began what was to become a perennial analysis of how I was spending my own time.
The other day I got to be the one wielding the tape measure in my own shop. It was for my 13-year-old son, who is in a great hurry to be driving and to have a job and an apartment and unlimited access to snacks. After my re-creation of the tape measure experience, I could see that my son was still rattling around, feeling ready for bigger and more, but I think he also heard me because he came back a few days later with a list of goals for this year, things he can do and work toward now. Things that embrace what is here before him rather than the imagined and desired future, representing a shift in focus that allows for seeing the bird of prey in the tree and not just the distant moon framed by the branches.
One of his goals was to climb the mountain beyond our back pasture, solo. And he did it. Looking ahead is important, I would tell him. And so is being in your life, fully, on the way there.